In-house casthouse, the heart of the company
Using state-of-the-art equipment and continuously modernizing and increasing our casting capacities, we are following the quality requirements of top clients. Furthermore, with our extensive metallurgical knowledge, which we are constantly upgrading since the inception of our company, we have developed numerous alloys that we semi-continuously cast in billets, rolling slabs, and cast bars. Currently, we have more than 230 various chemical compositions in our casting program, and the number is growing annually.
Expanded Range of Cast Bars – Quality and Flexibility in One Place
At the Impol Foundry in Slovenska Bistrica, we successfully invested in expanding our range of cast bar diameters. Alongside the two existing diameters, we have now achieved the first casting of 72 mm diameter bars. Our cast bars are now available in three different diameters:
- 72 mm,
- 82 mm,
- 107 mm.
After machining, we can offer final diameters ranging from 65 mm to 106 mm, providing greater flexibility to meet the needs of various industries.
Advantages of Our Cast Bars
Our cast bars offer:
- Comparable quality to extruded bars,
- Excellent machinability and reliability,
- Flexibility for a wide range of industrial applications.
Along with providing dimensional versatility, we produce bars in seven different alloys of the EN AW 6xxx series and can also cast them in accordance with customer requirements. This adaptability supports broad applications in forging and other demanding processes, such as:
- Classic forging,
- Hot forging,
- Impact extrusion,
- Various machining processes.
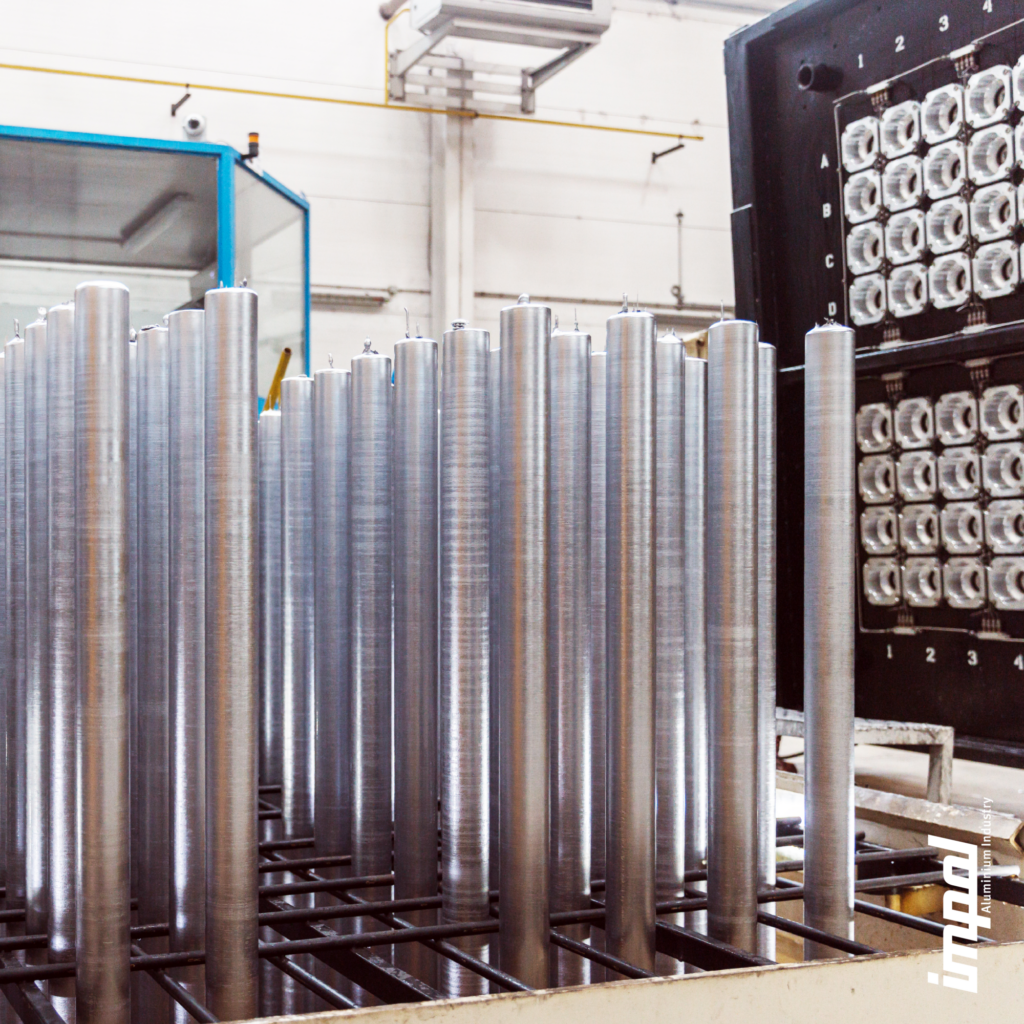
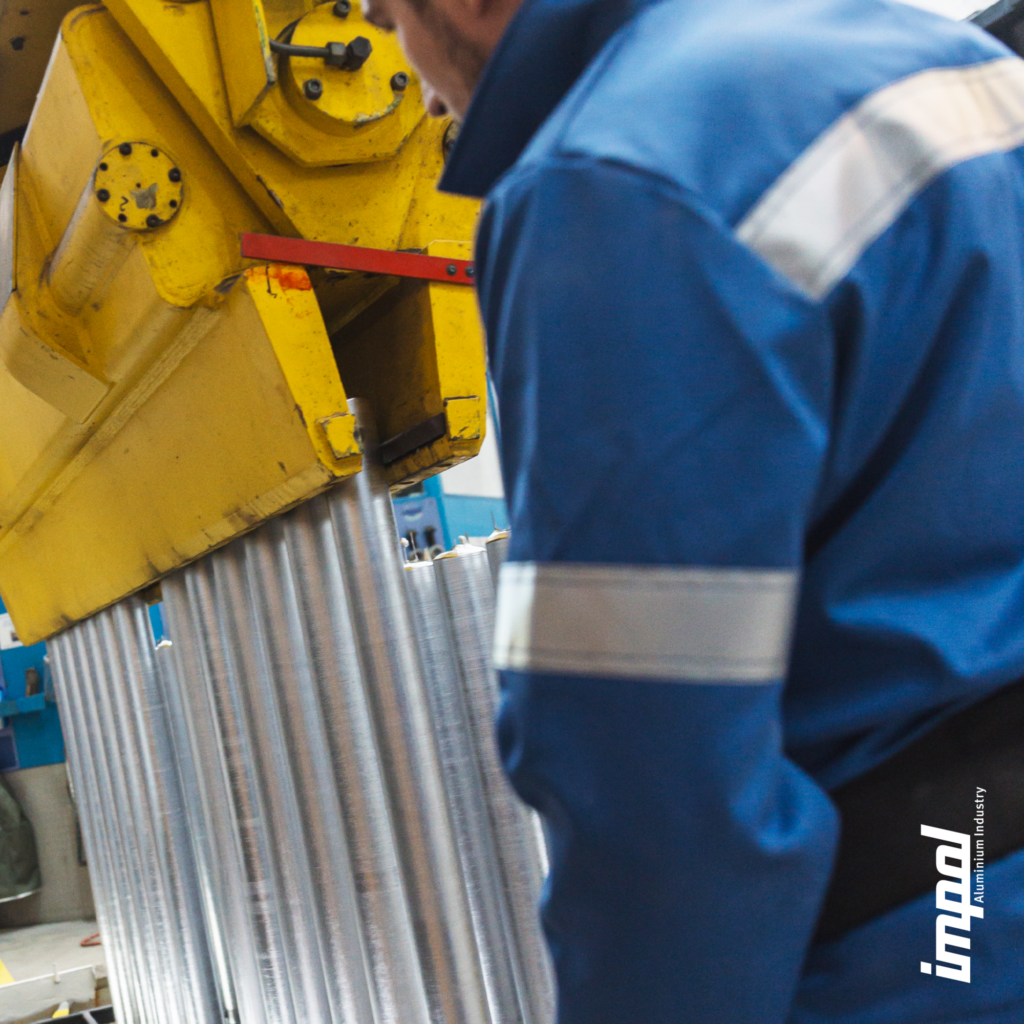
Technological progress and high performance
With state-of-the-art technologies and the expertise of our team, we ensure an annual production capacity of up to 35,000 tons of cast bars. Our processes are optimized to ensure the highest quality and adapt to specific customer needs.
Why to choose Impol’s cast products?
- Reliability: Our technology enables precise and consistent production of cast products.
- Flexibility: Various diameters and alloys cast to customer specifications for a wide range of applications.
- Quality: By using advanced casting processes, we achieve excellent product properties comparable to extruded products.
- Sustainability: Due to the shorter technological path, cast rod products provide a lower carbon footprint compared to extruded rods.
Contact Us
For more information about our cast products and collaboration opportunities, please contact us. Our team is ready to help you find a solution tailored to your specific needs.
Stronger and more efficient.
Our casthouses operate at three locations – in Slovenia, Serbia, and Croatia. The total cast product capacity exceeds 260,000 tonnes of our annual production. With numerous investments in modern technology, we are increasing the share of processing secondary aluminium and thus decreasing the negative environmental impact. Our casting lines are modern, digitalized, and enable full traceability of the produced material and comprehensive management of process parameters.

Quality
Comes first
After the casting and homogenization processes of billets are completed, they are also 100% controlled using an ultrasonic device that facilitates ultrasonic control of billets in compliance with the AMS MIL-STD-2154, Class B and A, and ASTM B594, Class B, and A standards.
In the years to come, the company will mainly increase the wide strip casting capacity, modernize the machinery, and increase its homogenization capacities.